Climate, circularity and water
A healthy earth is essential for us all. The key aspect of this pillar is to limit negative environmental impact as a means of counteracting the effects of climate change. This way we can enjoy our products today, as well as tomorrow. We are devoting our efforts to creating a circular world, in which there is no waste and no pollution. Our priority is reducing waste, water and our carbon footprint.
Healthy Earth
Our water consumption per tonne produced has fluctuated in recent years. With our renewed sustainability strategy we aim to focus greater attention on this and are aiming for a structural reduction over the coming years. Unfortunately, our scope 1 emissions have risen by 17% in comparison to the 2018 reference year. Despite all kinds of measures, we have as yet been unable to achieve an overall reduction. This is primarily due to growth caused by the addition of new production lines and the inefficient start-up of the Poperinge plant. By contrast, Aviko Rixona’s carbon footprint declined slightly in comparison to 2018. By generating our own electricity, reducing power consumption and purchasing green electricity, our scope 2 emissions significantly declined by 38%. This is primarily due to the switch to 100% green electricity for the majority of our plants.
In the future we will fully devote our efforts to reducing our footprint so as to comply with the Paris Agreement. In addition, we will devote more attention to reducing waste and food waste in the chain and will also make this measurable.
By generating our own electricity, reducing power consumption and purchasing green electricity, our scope 2 emissions significantly declined by 38%. This is primarily due to the switch to 100% green electricity for the majority of our plants.
Granules & Flakes
Chilled & Frozen
Onze doelen
Reducing carbon footprint
35%
reduction CO2 emissions in scope 1 (2030)*
Reducing carbon footprint
50%
reduction CO2 emissions in scope 1 (2030)*- Aviko Rixona
Reducing carbon footprint
100%
green energy: zero scope 2 emissions (2025)
Maximise circularity
Zero waste
(2025)
Reducing carbon footprint
Scope 3
reduction targets determined (2024)
Reducing carbon footprint
Net zero
scope 1, 2 and 3 (2050)
Maximise circularity
100%
recyclable packaging (2025)
Maximise circularity
50%
food waste halved (2030)*
Care for water
15%
reduction in water consumption per tonne produced (2025)*
Care for water
30%
reduction in water consumption per tonne produced (2025)*- Aviko Rixona
* versus 2018 reference year
Granules & Flakes
Chilled & Frozen
“Last year, due to the unrest in the world, it has become abundantly clear that the energy supply is not as secure as we previously may have thought. Our CO2 reduction projects consequently are more than welcome in these times and internally give us a boost by confirming that we are on the right track.”
Maikel van Bakel - Managing Director Aviko Rixona
Governance
Our Environmental Managers and Innovation Experts, in close cooperation with Plant Managers, have a key role in making our production processes sustainable. Together they look for ways of making production more energy efficient and increasingly making use of green energy.
In addition, reducing and reusing water and waste are important themes that are a high priority for them. In this respect we work in multidisciplinary teams using the TPM method. TPM or Total Productive Maintenance is an integrated method with the objective of improving business processes. In addition, we have created a special programme, SCO2RE, to reduce our carbon footprint. We use this programme to share knowledge within Cosun in order to tackle the challenges relating to the energy transition together and to learn from each other. In addition, our Packaging Managers and the commercial organisation are essential in maximising the circularity of our packaging and food streams.
We are reducing our carbon footprint
By optimising and greening our buildings and production processes we are able to reduce our carbon footprint. For example, we have the most sustainable cold store in the world, we are increasingly making use of green energy and we are working on making our transport more sustainable. With all of these initiatives, we are working hard on reducing our emissions.
Stories
Granules & Flakes
Chilled & Frozen
Chilled & Frozen
Most sustainable cold store in the world
We have the highest possible sustainability certification for our cold store in Steenderen (Netherlands): the BREEAM-NL* Outstanding certificate. This is because our cold store complies with the highest sustainability standards. With a score of 97.6% we are the proud owner of the most sustainable cold store in the world. We were also nominated for the international BREEAM Award, and placed a proud second...
Read more
Chilled & Frozen
Improved sustainability of transport
We make every effort to transport our products as efficiently as possible. As such we not only transport our products by road, but also by inland waterway and train, and, together with our carriers and partners, we are constantly looking for ways to do things more efficiently. Our efforts are not going unnoticed. We have won the Lean and Green Award and earned two Lean and Green stars. This means that we have achieved a 30% CO2 reduction in the field of logistics in comparison to 2010...
Read more
Chilled & Frozen
Reducing and greening energy use
We have been actively working on making our use of energy more sustainable since 2005. For example, we are focusing on making more efficient use of energy and on greening the energy that we do use. In 2018, the target we formulated was to reduce our gas consumption by 35% by 2030 (scope 1). To achieve this target, we are aiming for a minimum reduction of 3% each year. In addition, we aim to fully green the energy we are purchasing (scope 2). Our goal is for all of the electricity purchased by us to be 100% green by 2025...
Read more
Granules & Flakes
Reducing and greening energy use
Aviko Rixona has already made considerable progress in reducing and greening its energy use in recent years. Between 2006 and 2018 the plant in Venray (Netherlands) reduced its energy consumption per tonne of end-product by 15%, while the plant in Warffum (Netherlands) reduced it by no less than 30%. Aviko Rixona’s objective is to reduce its scope 1 emissions by 50% in comparison to 2018, by 2030. We are implementing a wide range of initiatives for this purpose.
Read more
Switch to more sustainable palm oil
We use vegetable oils, primarily palm and sunflower oil, to deep-fry our products. Palm oil is an efficient crop with a yield per hectare that is 4 to 10 times higher than sunflower oil. Unfortunately, palm oil is also linked to deforestation and the loss of biodiversity. Sunflower oil is a less efficient crop and requires more land, fertilisers and pesticides to produce the same quantity of oil. Due to developments in Ukraine, significantly less sunflower oil was available in 2022 and we therefore used more palm oil.
Read more
Dilemma: Growth versus reducing environmental impact
Aviko aims for growth. However, expanding our capacity has an impact on the environment, while it is our intent to limit that impact. This is why we are opting for the 'green by design' principle. For each project we meticulously identify the projected impact on the environment and how we can ensure this impact, in the design phase, can be as green as possible.
We maximise circularity
By making even more efficient use of our raw materials, we are able to further minimise waste. We aim to use and valorise 100% of the potato. We are currently making significant progress in various areas: we avoid food waste by giving our co-products a new purpose. Furthermore, we are always looking for more sustainable ways of packaging our products as a means of further reducing waste within the chain.
Stories
Granules & Flakes
Chilled & Frozen
Chilled & Frozen
100% recyclable packaging
At Aviko we use tens of thousands of tonnes of packaging materials for our chilled and frozen products. We can therefore have a tremendous impact by making our packaging more sustainable. We pay attention to reducing packaging materials and whether the materials that we do use are recyclable.
At the present time, 84% of our primary packaging materials is recyclable; a minor increase of 2% in comparison to last year. While this is a nice accomplishment, our ambition reaches beyond this. Our goal is for our packaging materials to be 100% recyclable by 2025. We work together with suppliers to develop mono-plastics that are easier to recycle compared to the combination of different materials we are still using in some instances. For example, since 2022, all Aviko packaging in Dutch supermarkets is recyclable...
Read more
Granules & Flakes
100% recyclable packaging
In the production of granules and flakes we produce millions of consumer packages of potato puree for various large A-brand manufacturers, retailers and foodservice customers. At the present time, 79% of our primary packaging materials are recyclable. Unfortunately, this is a slight decrease of 2% in comparison to last year and the millions of metres of metallised film we use are not yet recyclable. We have agreed with a number of our major customers that we will be using 100% recyclable film starting in 2025. This is subject to the condition that this recyclable film must continue to meet all of the quality criteria of our packaging, so that this does not lead to food waste. This way we are working, together with suppliers, on the challenge of developing recyclable film that will not adversely affect the shelf life of potato puree, as that would lead to unnecessary food waste.
No potato waste but maximum valorisation
We avoid wasting food by making optimal use of all co-products that are created during the production of fries and other potato products. Duynie, an Aviko sister company within the Cosun Group, uses residual flows to produce high-quality products, thus enabling us to use and valorise the entire potato. For example, we extract starch from our process water that is then processed into high-quality starch for various innovative applications, such as packaging materials and wallpaper glue. In addition, shreds that are left over after the potatoes are cut are processed into specialty products as much as possible. When they are not suitable for this purpose, they are sold as high-quality animal feed in cooperation with Duynie. This way we make a contribution to the transition to a circular food system and furthermore reduce food waste and the carbon footprint within the chain.
Read more
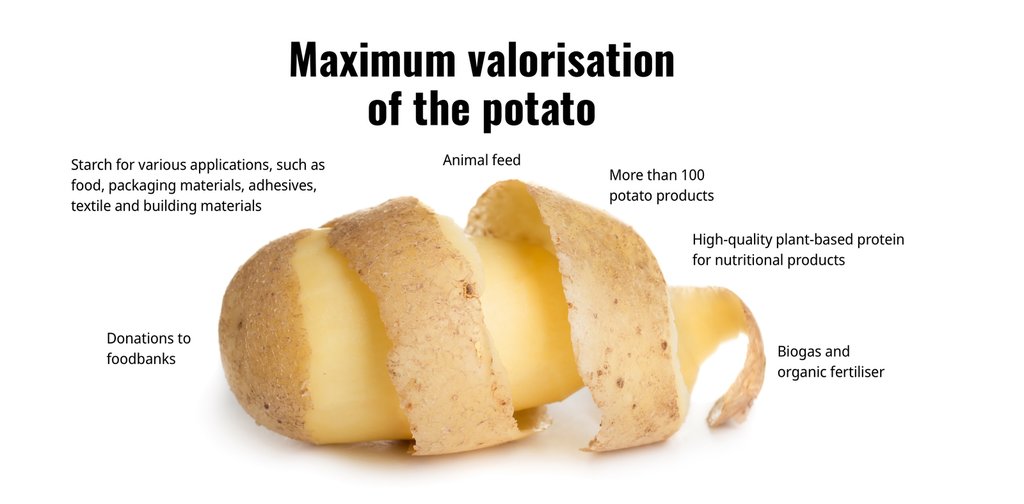
Dilemma: Food, feed or fuel
We regularly debate what is best: further valorising the co-productsproduced by processing our potatoes into food (food for people), feed(livestock feed) or fuel (biomass for energy production). Where possible we try to make use of our co-products for human food. The world is confronted with the enormous challenge of feeding a growing population, while at the same time making a transition to green energy with due haste. At Aviko, we use co-products for food, feed, as well as fuel and make a balanced assessment each time in this respect.
We take care of water
We are reducing our water consumption and treat used water so it can be reused.
Stories
Granules & Flakes
Chilled & Frozen
Granules & Flakes
Optimal use and reuse of water
For us, no waste also means using as little water as possible and to treat and reuse as much water as possible. Aviko Rixona aims to achieve a reduction of 30% of its water consumption per tonne of product produced. In 2022, a reduction roadmap was developed for this purpose. Our methane reactor with water treatment at the plant in Venray (Netherlands) is a great example of optimally using and reusing water. The water treatment purifies the process water using bacteria that eat the organic substances. This process requires a great deal of oxygen, which in turn consumes electricity. Thanks to our methane reactor we are now able to purify water using an oxygen-free and energy efficient method. This process also produces biogas, which is used in the plant. We therefore achieved gains in two areas: we reduced our consumption of natural gas, and the water is more efficiently purified, and we can also reuse a large part of this water. For example, the e-boiler requires ultra-pure water, which will be made in a circular process using the water from our water treatment facility.
Chilled & Frozen
Most sustainable cold store in the world
We have the highest possible sustainability certification for our cold store in Steenderen (Netherlands): the BREEAM-NL* Outstanding certificate. This is because our cold store complies with the highest sustainability standards. With a score of 97.6% we are the proud owner of the most sustainable cold store in the world. We were also nominated for the international BREEAM Award, and placed a proud second.
There are more than 2,700 solar panels on the roof of the cold store. The cold store functions as a flexible battery by regulating temperature in accordance with weather conditions: a higher temperature setting when there is less sun and lower temperature during nice weather when there is excess energy. Water-saving measures are implemented in the cold store itself; for instance, rainwater is collected for internal use. In addition, we have placed insect hotels and created breeding places and dwellings for bats and birds in the proximity of the cold store in order to promote biodiversity.
In 2022, in Poperinge (Belgium) we opened one of the world’s most efficient fries production plants with the least possible waste and highest possible energy efficiency. The cold store in Poperinge has been built in accordance with the BREEAM standards used for our sustainable cold store in Steenderen, we use solar panels for power generation, and reuse heat and water to the maximum possible extent. We reuse 15% of the process water after treatment at the plant’s location itself. In addition, we generate biogas during the water treatment process that we use as energy for the plant’s production process, which in turn results in a 10% reduction in our energy use.
* BREEAM stands for Building Research Establishment Environmental Assessment Method, a global benchmark for establishing the sustainability of buildings. The method assesses almost every building aspect, including construction, materials, energy, transport, waste, pollution, water, land use and ecology.
Chilled & Frozen
Improved sustainability of transport
We make every effort to transport our products as efficiently as possible. As such we not only transport our products by road, but also by inland waterway and train, and, together with our carriers and partners, we are constantly looking for ways to do things more efficiently. Our efforts are not going unnoticed. We have won the Lean and Green Award and earned two Lean and Green stars. This means that we have achieved a 30% CO2 reduction in the field of logistics in comparison to 2010.
Much of our transport is by road. We are making progress in making this more sustainable
Much of our transport is by road. We are making progress in making this more sustainable, for example by optimising loads: as a result, we are transporting more with less CO2 emissions. In addition, Aviko, together with partners, is also working on innovations relating to electric transport. In Steenderen (Netherlands) an ultramodern Automated Guided Vehicle (AGV) is transporting our products from the plant to our sustainable cold store. This is a first in the Netherlands, and was achieved in cooperation with VDL and the Province of Gelderland. This self-driving truck transports fully electrically cooled products and is unique in the world.
In 2022, we worked hard on an electrically driven truck pilot. In 2023, in cooperation with Doesburg Container Terminal we are going to put an electric truck into operation for transporting containers between our plant in Steenderen and the port of Doesburg. From there the containers are transported to their ultimate destination by inland waterway, which emits less CO2 in comparison to road transport. We also make use of trains for the transport of goods to Southern and Eastern Europe. In addition, we are working closely with our pallet pool partner CHEP on optimising our logistics and making circular use of our pallets by reusing them. This not only represents a major reduction in wood use, it also results in an 890 tonne reduction in CO2 emissions because of the elimination of the return transport of used pallets.
Chilled & Frozen
Reducing and greening energy use
We have been actively working on making our use of energy more sustainable since 2005. For example, we are focusing on making more efficient use of energy and on greening the energy that we do use. In 2018, the target we formulated was to reduce our gas consumption by 35% by 2030 (scope 1). To achieve this target, we are aiming for a minimum reduction of 3% each year. In addition, we aim to fully green the energy we are purchasing (scope 2). Our goal is for all of the electricity purchased by us to be 100% green by 2025. The electricity we are currently purchasing for all Chilled & Frozen plants in Europe has been green since 2022. In some areas the infrastructure needed to meet future green energy demand is insufficient. We are in discussion with grid operators, municipalities and provinces for this purpose in order to accelerate the energy transition.
The production of fries releases a lot of residual heat. We are trying to reuse this residual heat as effectively as possible. For example, we are using it in our blanching, drying and cleaning production processes. The residual heat produced by our plant in Steenderen (Netherlands) is used to heat the local swimming pool, sports hall and school. This way we create joy for our neighbours, the local community and the environment.
At Aviko in Sweden we use the residual heat of our cold storage in the plant. This has enabled us to stop using natural gas. Production there now is climate-neutral as we are now only using green electricity here.
Our plant in Rain (Germany) operates virtually climate-neutral as well. The plant makes use of the energy generated by the adjacent biomass plant. This plant converts local waste wood into green energy.
Unfortunately, we are not as far advanced in our two plants in China. Our focus there is on phasing out coal as a source of energy. We are now working together with various parties to investigate the possibilities for achieving this on the basis of the available energy infrastructure. In addition, in cooperation with an external consulting firm, we are investigating how we can further improve the environmental performance of our Chinese plants. Efficiency here has significantly improved in recent years with a 40% reduction in water and CO2 per tonne of product produced. We continue working on improvement projects relating to energy and water efficiency here in order to bring the plants up to the same level as that of our European plants.
Granules & Flakes
Reducing and greening energy use
Aviko Rixona has already made considerable progress in reducing and greening its energy use in recent years. Between 2006 and 2018 the plant in Venray (Netherlands) reduced its energy consumption per tonne of end-product by 15%, while the plant in Warffum (Netherlands) reduced it by no less than 30%. Aviko Rixona’s objective is to reduce its scope 1 emissions by 50% in comparison to 2018, by 2030. We are implementing a wide range of initiatives for this purpose.
In our plant in Warffum (Netherlands) an industrial heat pump was recently put into operation that will result in a reduction of over 1,100 tonnes of CO2 per year. The residual heat that previously was lost in the environment will now be used for the production process, thus reducing the natural gas needed for this purpose. This results in a savings of over 650,000 cubic metres of gas (7% of Warffum's gas consumption) and the cooling system has been deactivated as a result of which there no longer is a need for electricity. Our plant in Stavenhagen (Germany) runs on the energy supplied by the adjacent power plant. This plant converts local, sorted waste into approximately 50% green energy.
“II like to devote myself fully to mixing Aviko’s iconic blue and yellow colours into a sustainable green. We can only do this together!”
Jeroen Zwietering - Process Engineer Energy Aviko Rixona
In Venray (Netherlands) we recently installed two blow-off condensers on the peeling lines that are used to partly recover the energy of the peels after which it can be used for the granule lines. This is expected to result in savings of 800,000 cubic metres of natural gas over time. By producing biogas in our water treatment process in Venray, we saved approximately 500,000 cubic metres of natural gas in 2022.
In 2022, Aviko Rixona invested in a 30 megawatt industrial electric boiler for its plant in Venray (Netherlands). Currently the required demand for heat is still being provided by means of burning natural gas. The steam boilers in Venray are responsible for approximately 70% of the total gas consumption and as such account for a significant portion of the scope 1 CO2 emissions. The use of the new e-boiler creates a hybrid steam system and during a minimum of 3,000 hours each year it will now be possible to generate high-quality heat using green electricity. This will reduce gas consumption by 46% in comparison to the 2018 reference year, or a reduction of 17,700 tonnes of CO2 per year. Furthermore, generating sustainable heat using this e-boiler will reduce the emission of nitrogen oxides by approximately 38%. The e-boiler will be constructed in 2023 and is expected to be operational in 2024.
Switch to more sustainable palm oil
We use vegetable oils, primarily palm and sunflower oil, to deep-fry our products. Palm oil is an efficient crop with a yield per hectare that is 4 to 10 times higher than sunflower oil. Unfortunately, palm oil is also linked to deforestation and the loss of biodiversity. Sunflower oil is a less efficient crop and requires more land, fertilisers and pesticides to produce the same quantity of oil. Due to developments in Ukraine, significantly less sunflower oil was available in 2022 and we therefore used more palm oil.
We have taken further responsibility for making the palm oil industry sustainable and in Europe we have switched over from ‘book and claim’ palm oil to fully 'segregated' certified palm oil. In 2022, we made the necessary preparations for this switch and effective from 1 January 2023 we are only using segregated certified palm oil. This is sustainable palm oil that is harvested and shipped fully segregated and that is not mixed with less sustainable palm oil. This way we ensure that our products only contain sustainable palm oil. The international Roundtable on Sustainable Palm Oil (RSPO) was founded to achieve a generic standard for sustainable palm oil. Aviko is member of the RSPO in order to further stimulate the production of sustainable palm oil. Certified palm oil protects the environment and the local communities that depend on this for their livelihood, so that palm oil can continue to play an important role in food security.
“The Dutch Alliance for Sustainable Palm Oil (DASPO) is a partnership of parties established in the Netherlands that are involved in the palm oil chain. The objective is to jointly achieve 100% deforestation-free and sustainable palm oil in the Netherlands. Together with our members we are actively countering deforestation, giving small-scale farmers a fair chance and we are working on a transformation of the industry. It is good to see that Aviko, together with us, is focusing its efforts on creating a sustainable palm oil chain. Together we make the difference!”
Eddy Esselink - Program Manager Sustainable Development MVO + Chair DASPO
Chilled & Frozen
100% recyclable packaging
At Aviko we use tens of thousands of tonnes of packaging materials for our chilled and frozen products. We can therefore have a tremendous impact by making our packaging more sustainable. We pay attention to reducing packaging materials and whether the materials that we do use are recyclable.
At the present time, 84% of our primary packaging materials is recyclable; a minor increase of 2% in comparison to last year. While this is a nice accomplishment, our ambition reaches beyond this. Our goal is for our packaging materials to be 100% recyclable by 2025. We work together with suppliers to develop mono-plastics that are easier to recycle compared to the combination of different materials we are still using in some instances. For example, since 2022, all Aviko packaging in Dutch supermarkets is recyclable.
At the present time, 84% of our primary packaging materials is recyclable.
In addition to making packaging materials recyclable, we are also devoting effort to reducing the volume of packaging materials. For example, we are using thinner cardboard for all of our products packed in boxes. This has resulted in a reduction of 100 tonnes of cardboard per year and in 4,800 fewer pallet movements. In other words, we are using less cardboard to package more products. Furthermore, by making use of thinner film for vacuum-packed products we reduced the use of plastics by 20 tonnes annually. In Sweden we are using a system of returns with plastic crates for affiliated customers, thus enabling us to reduce the number of cardboard boxes. Moreover, 100% of our secondary packaging, such as boxes, is already recyclable.
No potato waste but maximum valorisation
We avoid wasting food by making optimal use of all co-products that are created during the production of fries and other potato products. Duynie, an Aviko sister company within the Cosun Group, uses residual flows to produce high-quality products, thus enabling us to use and valorise the entire potato. For example, we extract starch from our process water that is then processed into high-quality starch for various innovative applications, such as packaging materials and wallpaper glue. In addition, shreds that are left over after the potatoes are cut are processed into specialty products as much as possible. When they are not suitable for this purpose, they are sold as high-quality animal feed in cooperation with Duynie. This way we make a contribution to the transition to a circular food system and furthermore reduce food waste and the carbon footprint within the chain.
“Duynie is working together with Aviko on the circular valorisation of co-products for various applications. One of these applications is circular livestock feed, which makes a contribution to circular agriculture and making the meat, dairy and potato chain more sustainable. This way we create value for our suppliers, customers and the planet.”
Frank Waijers - Managing Director - Duynie Feed Benelux